Hand Planes: A Detailed Guide to Types and Use
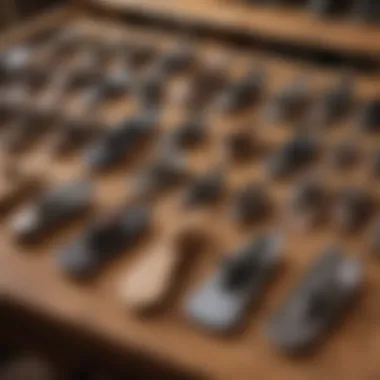
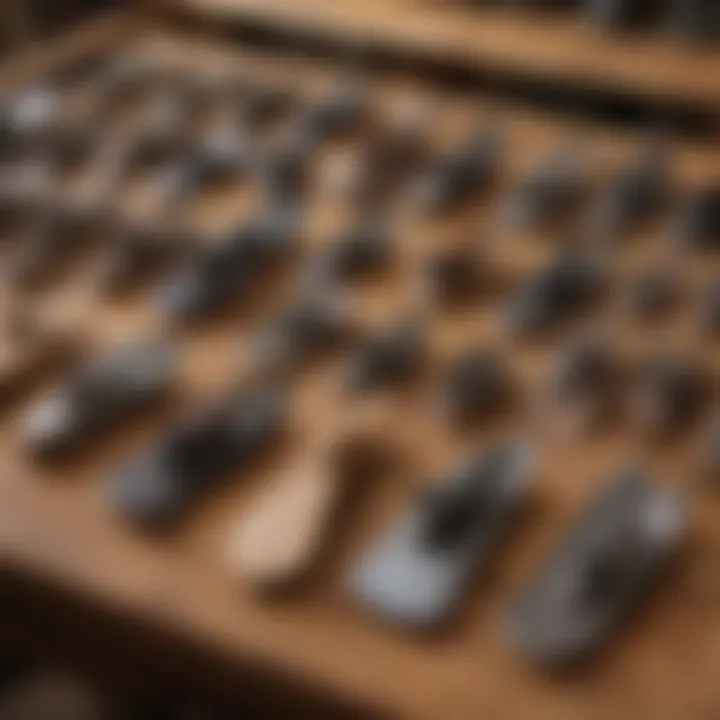
Intro
Hand planes are often overlooked tools, yet they offer a timeless elegance and unparalleled precision in woodworking, particularly for those who are serious about their craft. From the ancient artisans who first shaped wood to modern-day surfboard shapers seeking to perfect their designs, hand planes have carved a significant niche in various fields.
In this exploration, we will dig into the nuances of hand planes, examining their history, types, and important functionalities. We will also discuss how these tools are essential in the art of surfboard shaping, bridging the gap between classic techniques and contemporary demands. By the end, readers will have a comprehensive toolkit of knowledge, enabling them to select the appropriate hand plane, maintain it effectively, and utilize it skillfully.
Gear and Equipment
To create surfboards that dance over waves with grace, shapers must harness an array of tools. Among these, hand planes stand out, not just for their effectiveness but also for their craftsmanship. When discussing gear and equipment for surfboard shaping, understanding the specific tools and technologies makes all the difference.
Latest Surfboard Technologies
The surfboard industry has seen a rapid evolution of technologies, blending tradition with innovation. Hand planes, especially those made from high-quality hardwood like mahogany or maple, provide an unmatched tactile feedback that modern machines can't replicate. Shapers are increasingly embracing traditional planing techniques as a way to produce boards that not only perform better but also have a unique character.
Moreover, advancements like lightweight epoxy resins and intricate shaping software are now often paired with hand planing. This harmony of old and new allows shapers to mold surfboards that suit personal styles while remaining functional in various wave conditions.
Essential Accessories for Every Surfer
A well-equipped surfboard shaper wouldn’t just stop at the plane itself. To achieve the finest results, a range of accessories comes into play:
- Level and Square: For accurate markings and angles.
- Dust Masks: Protect your health while working with fine wood particles.
- Sanding Blocks: These create smooth finishes that complement the work done with hand planes.
- Clamps: Essential for holding your project steady during shaping.
With these tools and accessories at hand, shapers can elevate their craftsmanship and ensure their surfboards feel personal and precise on the water.
"The beauty of surfboard shaping lies in the connection between the craftsman and his tools; each plane holds a story of its own."
Surf Techniques and Skills
While hand planes are integral to shaping surfboards, the techniques and skills involved in surfing itself cannot be understated. Successful surfers develop a tactile understanding of their boards, forged not just from experience but from how the shape and finish affect performance.
Beginner Surfing Techniques
For those starting out, focus on the basics. Balancing on the board, understanding wave patterns, and paddling techniques set the groundwork. One fundamental skill involves catching waves at the right time, known as timing. The shape of your surfboard, heavily influenced by the shaper's hand plane work, impacts how effectively a beginner can link with waves.
Advanced Maneuvers for Experienced Surfers
As surfers progress, they begin to understand the subtleties of their craft. They learn about turns, cutbacks, and aerial maneuvers, all of which depend heavily on the design nuances achieved during the shaping process. A board shaped by a skilled craftsman with well-tuned hand planes allows for sharper turns and increased responsiveness on the wave.
In this comprehensive view of both hand planes and surfing, we need to recognize that a symbiotic relationship exists between the two. The right tools enhance the creation of bespoke surfboards, and conversely, understanding surf techniques enriches the purpose of those surfboards.
This exploration of hand planes will provide readers with an insightful perspective, whether they are woodworking enthusiasts aiming for mastery or surfboard shapers crafting their next wave riding tool.
Prologue to Hand Planes
In the realm of woodworking, there exists a set of tools as pivotal as the hammer or chisel: hand planes. While often overshadowed by power tools, hand planes offer a level of precision and finesse that can elevate a project from ordinary to extraordinary. Understanding their place in both traditional and modern woodworking contexts is vital for anyone serious about the craft.
Using a hand plane means embracing a tactile, almost meditative approach to shaping wood. This tool enables artisans to fine-tune the surface of boards, create intricate profiles, and even effectuate joinery—all while fostering a connection with the material that many electric tools simply can't match. Whether you're smoothing a rough plank or crafting delicate curves, hand planes are an extension of your hands, translating intention into form.
Understanding the Functionality
At its core, a hand plane's function is deceptively simple: it shaves off thin layers of wood. However, the implications of this action are profound. Woodworkers employ a variety of hand planes, each designed for specific tasks. For instance, a smoothing plane excels at preparing surfaces for finishing, providing a glass-like sheen. On the other hand, a jack plane is often used for initial flattening, making it a versatile starter tool in any woodshop.
The mechanics behind a hand plane involve the blade, or iron, fitted at an angle to the base, or sole. As the plane glides over the wood's surface, the blade slices through fibers, leaving behind a smooth finish. Adjustments can be made to control depth and angle, giving woodworkers the ability to fine-tune their results. Learning these adjustments takes practice, but it leads to greater control and ultimately better craftsmanship.
Historical Overview
Hand planes have a storied history dating back thousands of years, with their origins tracing to ancient times. Early examples were rudimentary, resembling nothing more than a sharpened stick used to scrape surfaces. Over time, as woodworking evolved, so did the design and functionality of hand planes. By the Middle Ages, more sophisticated metal planes emerged in Europe, often adorned with unique designs and craftsmanship.
In the 19th century, with the rise of industrialization, hand planes saw significant changes. Mass production techniques made these tools more accessible to the average carpenter, but some craftsmen remained devoted to the meticulous hand-crafted models. The debate over the superiority of hand tools versus machinery is still alive in today's woodworking community, with proponents of both sides arguing passionately for their chosen methods.
Hand planes continue to hold a respected place in woodworking traditions around the globe. They represent not just tools, but a legacy of craftsmanship passed down through generations, showcasing the union of function and art in woodworking.
Types of Hand Planes
Understanding the various types of hand planes is crucial for both woodworking enthusiasts and surfboard shapers. Each type serves a distinct purpose, and recognizing these differences can greatly enhance craftsmanship and precision in any project. By differentiating between their characteristics, you can select the proper tool that aligns with your specific needs, leading to improved results and satisfaction in your work.
Bench Planes
Characteristics and Uses
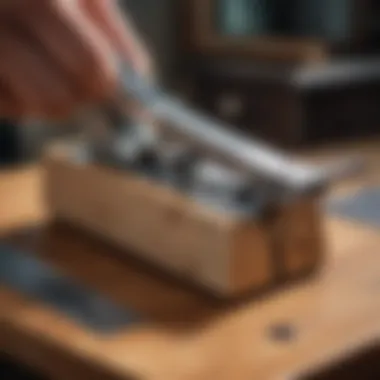
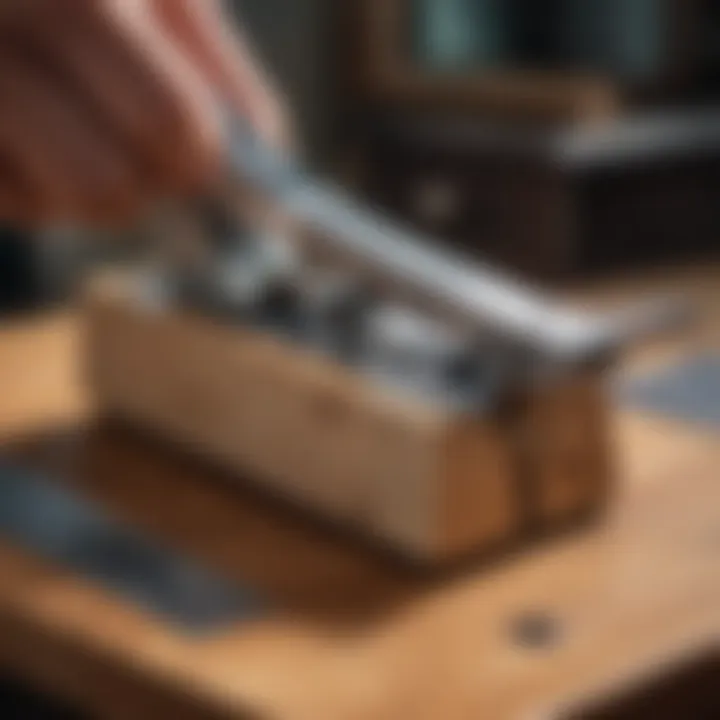
Bench planes are the workhorses of woodworking. They come in different sizes, from the commonly used No. 4 smoothing plane to larger No. 7 jointers. Their primary role is to flatten and smooth the surface of wood, making them indispensable in any woodworker's arsenal. The long flat surface of a bench plane allows for an even distribution of pressure, resulting in a level finish.
This characteristic makes bench planes especially effective for preliminary shaping and refinement of lumber.
The adjustability of the blade depth is another key feature that gives them versatility for various tasks—whether you want to take aggressive shavings off rough boards or perform delicate smoothing operations.
However, one drawback that beginners may face is the initial learning curve. It can take time to master the control and technique needed to achieve optimal results with a bench plane.
Popular Models
When exploring popular models, the Stanley No. 4 is often the go-to choice for many woodworkers, thanks to its balance and manageability. This plane is lauded for its ease of use and effectiveness in smoothing out surfaces without creating tear-out, allowing finer finishes than you may get with power tools alone. Another highly regarded model is the Lie-Nielsen No. 62, known for its precision engineering and sturdy construction. Though on the pricier side, many artisans swear by it for its durability and efficiency.
These models highlight a trend where quality often trumps price, suggesting that investing in quality hand planes can yield greater satisfaction and outcomes in your woodworking projects.
Block Planes
Design Features
Block planes are compact and portable, easily fitting into any toolbox. Designed primarily for trimming and shaping, their unique low-angle cutter allows for slicing across the grain with less chance of tear-out. A key aspect of block planes is their versatility; they can handle various angles of wood grain, making them excellent for both edge work and finish smoothing.
Most block planes also feature a thumb lever, which allows quick adjustments on the go. However, their small size can limit their ability to handle larger pieces of wood as effectively as larger planes do.
Applications in Woodworking
Block planes shine particularly in detail work, making them a favorite among cabinet makers and finish carpenters. Whether it’s for chamfering edges or making minuscule adjustments to a joint fit, these tools deliver precision. While they may not be the first tool that comes to mind when starting a woodworking project, their role is invaluable in fine-tuning pieces or performing delicate shaping. There’s something satisfying about wielding a block plane delicately; the control it offers results in cleaner edges and smoother finishes, enhancing the overall quality of your work.
Specialty Planes
Types and Functions
Specialty planes include a range of tools designed for specific tasks—think of them as the Swiss Army knives of hand planes. Types of specialty planes can include rabbet planes, dado planes, and even curved planes for specific shaping needs. Each has a thoughtful design that allows for specific functions, such as creating grooves or shaping rounded edges. This makes them both unique and beneficial in their own right for specialized woodworking applications. The downside, though, is that these planes can sometimes be less versatile than general types, leading to a more focused range of applications.
Unique Benefits
The unique benefits of specialty planes are their ability to deliver precision on specific tasks that general types may struggle with. For example, a rabbet plane is ideal for cutting notches or grooves, which can be crucial for joinery. While you may not reach for a specialty plane as often as a bench or block plane, its precise capabilities can save a project from unnecessary frustration.
Furthermore, using a specialty plane can often yield craftsmanship that is not just functional but elevates the aesthetic of the finished piece, drawing admiration from both woodworkers and spectators alike.
Selecting the Right Hand Plane
Choosing the right hand plane is pivotal for achieving quality results in woodworking and surfboard shaping. Each type of hand plane serves a specific purpose, and understanding their nuances can elevate your craftsmanship. Whether you're a seasoned professional or a weekend warrior, making an informed decision can save you time and frustration while improving the quality of your work. Let's dissect the critical elements to consider when selecting the right hand plane tailored to your projects.
Considerations for Use
Material Types
When it comes to material types, think of it as the backbone of every hand plane. Hand planes can be crafted from various materials, including cast iron, aluminum, and wood. Cast iron models are often praised for their durability and stability. They hold their adjustments well and resist warping over time. On the flip side, aluminum models offer a lightweight alternative which can be easier to maneuver, particularly for detailed tasks.
One of the unique features of cast iron planes is their ability to maintain a flat surface over years. They tend to absorb vibrations, allowing for smoother operations. However, they also come with a heavier profile, which might not suit every user's preference. In contrast, while aluminum is easier to carry, it might not provide the same level of precision over the long haul.
In terms of advantages and disadvantages:
- Cast Iron: Durable, heavy, holds adjustments well
- Aluminum: Lightweight, easier to handle, might compromise durability
Woodworking Projects
Moving on to woodworking projects, the type of hand plane you choose can significantly affect the outcome of your work. Different projects require different hand planes. For instance, if you're working on delicate joinery, a block plane might fit the bill perfectly. On the other hand, for larger surfaces, a bench plane would be more appropriate.
The key to choosing wisely here lies in understanding your project's scope. Perhaps you need to mitigate rough edges or create intricate designs; selecting the right tool aids in both efficiency and craftsmanship.
One unique feature worth noting is how specialized planes can be tailored for specific tasks. This specificity can lead to finer details and more satisfactory finishes. However, acquiring too many specialized planes can clutter your workspace and complicate your toolkit, serving as a challenge for those with limited storage and budgets.
Advantages and disadvantages of selecting for projects:
- Specialized Planes: Offer high precision for particular tasks
- General Purpose: More versatile but might not excel in specific applications
Ergonomics and Comfort
Grip Styles
Next up, let’s talk about grip styles—a detail often overlooked, yet integral to your experience with hand planes. The way a tool feels in your hand can determine how effectively you work. Whether you prefer a classic knob grip or a more comfortable palm grip can make all the difference. A well-designed grip style allows a user to maintain control and stability during operation.
Some grips are designed with contours to fit the hand better, reducing strain during extended use. A poor grip, on the other hand, can lead to fatigue or even injuries over time, impacting your performance and enjoyment of woodworking.
- Contoured Grips: Provides comfort during long projects.
- Straight Grips: Simpler but can be tiring in prolonged use.
Weight Balance
Finally, we arrive at weight balance, which can influence the precision of your cuts. Too much weight at one end can lead to uneven pressure, while a well-balanced plane allows for a smoother glide over wood surfaces.
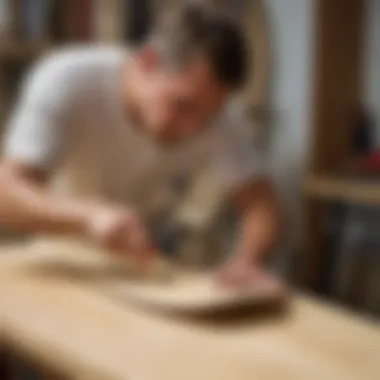
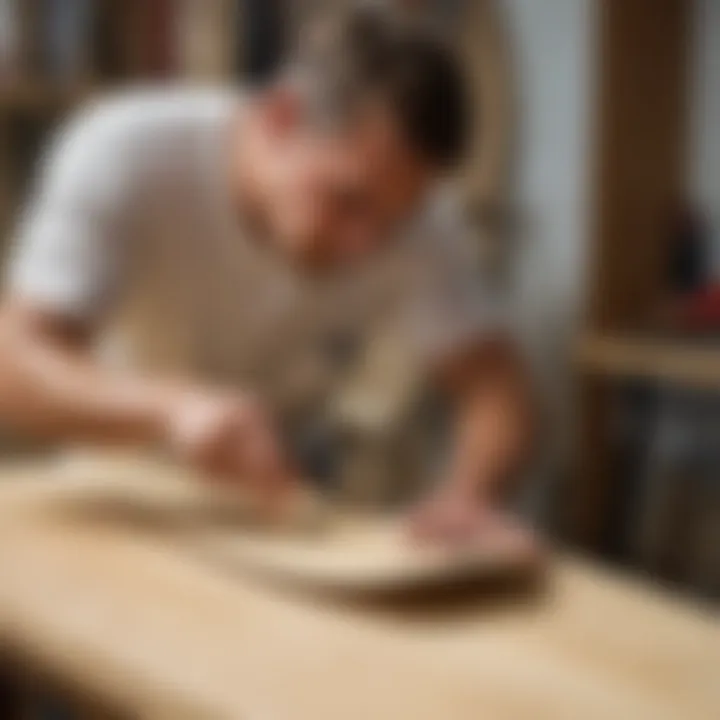
One key characteristic to focus on is how the distribution of weight affects maneuverability. Ideally, the user should feel as if the plane becomes an extension of their hand. If weight balance is off, it can lead to less control, making projects more arduous.
The unique feature of a well-balanced plane is its ability to allow for fluid movements, which can be crucial in scenarios requiring delicate adjustments or detailed joinery. However, overly heavy planes may suit experienced users but be cumbersome for novices.
- Adequately Balanced: Provides smoother operation and easy control
- Overly Heavy: Can lead to fatigue and lessen precision
Understanding the nuances of selecting the right hand plane enhances your ability to tackle various woodworking projects confidently and effectively.
Hand Plane Techniques
Hand plane techniques are foundational to achieving precision in woodworking. Proper technique not only affects the quality of the finished piece but it also ensures a smoother workflow, promoting efficiency and an overall positive woodworking experience. These techniques can be divided into two main categories: basic operations and advanced applications. Each of these holds unique nuances that every serious woodworker should grasp to fully leverage the potential of their tools.
Basic Operations
Planning Surfaces
Planning surfaces is one of the most vital operations conducted with hand planes. This process creates a flat and smooth surface, which is essential for any woodworking project. A key characteristic of planning surfaces is the ability to remove high spots on a workpiece, which leads to a uniform thickness. This process is particularly beneficial because it lays the groundwork for more intricate tasks, such as joinery and finishing.
One unique feature of planning is the adjustments available in the plane's iron (or blade) depth. This allows the user to precisely control how much material is removed with each pass. The advantage lies in the ability to take fine shavings for a smoother finish, while heavier cuts can be made when more drastic material removal is necessary. The downside, however, might be the learning curve involved; it can take some time to get the hang of matching the pressure and angle to the type of wood and condition of the workpiece.
Creating Edge Profiles
Creating edge profiles is another essential technique that holds its own in the woodworking world. This method allows woodworkers to shape the edges of their pieces, adding aesthetic qualities and functionality. A significant aspect here is the versatility of edge profiles, ranging from simple bevels to intricate designs. This aspect makes it a popular choice, especially in furniture making and cabinetry.
What sets this technique apart is the tools' design, including skewed blades that can create seamless curves or chamfers, enhancing the beauty of the finished product. The advantages of creating edge profiles include its applicability to various types of wood and projects. However, it requires a steady hand and can be time-consuming, particularly for complex designs.
Advanced Techniques
Smoothing and Finishing
When it comes to smoothing and finishing, this technique plays a pivotal role in delivering that flawless look to woodworking projects. It involves the use of specialized planes designed to remove minor imperfections, resulting in an exceptionally fine surface. This quality makes smoothing and finishing a critical step, especially for pieces meant for display or fine furniture.
The key characteristic of this technique is its focus on aesthetics and tactile quality, often resulting in a finish that feels as good as it looks. The unique advantage is the ability to achieve glass-like surfaces using very thin shavings. The flip side is that it can be tedious, requiring patience and experience to master the technique.
Joinery Applications
Joinery applications represent another advanced area where hand planes shine. This technique involves preparing joints that will hold pieces together, crucial for any wood-based project. Its importance cannot be overstated, as the quality of joinery often determines the strength and durability of the final product.
What distinguishes joinery applications is the precision required in cutting mortises, tenons, and other joint types. The benefit lies in the strength of the connections, which contribute to the piece’s overall integrity. However, achieving this precision can be challenging, particularly for beginners who might struggle with aligning their cuts cleanly.
In summary, mastering hand plane techniques not only significantly enhances the quality of woodworking projects but also empowers woodworkers with the ability to create beautiful, functional pieces. As much as it is about technique, it is about feeling confident in the skills required to express creativity through craftsmanship.
Maintenance of Hand Planes
Proper maintenance of hand planes is paramount in ensuring their longevity and performance. These tools, integral for achieving smooth, precise surfaces in woodworking, require a little attention and know-how to operate at their best. Neglecting proper care can lead to dull blades, rust, and reduced efficiency, which ultimately stifles creativity in a craft where precision is key.
Sharpening Techniques
Tools Required
When it comes to sharpening your hand plane, the right tools make all the difference. Essential sharpening tools include:
- Sharpening Stones: These come in varying grits, allowing for rough shaping and fine honing of the blade’s edge.
- Honing Guides: They aid in maintaining a consistent angle while sharpening, which is crucial for achieving a keen edge.
- Diamond Plates: Known for their durability and fast action, these plates can restore an edge quickly.
Using a honing guide can profoundly enhance the process, as it helps prevent variation in angles. Without it, even slight discrepancies can lead to an edge that performs far below potential. However, a downside to honing guides is the learning curve they may present for beginners. Gaining the knack for using them effectively will pay dividends in the long haul.
Best Practices
Adopting best practices during the sharpening process can significantly affect the efficiency of your hand planes. Here are some recommendations:
- Maintain Consistent Angles: Striving for consistency helps in achieving a sharper blade, which facilitates better cuts and easier maneuverability.
- Regularly Clean Blades: Keeping the blade free of resin buildup and debris can prevent unwanted wear.
- Practice Patience: Rushing through the sharpening process can lead to mistakes; take time to ensure thoroughness.
Adopting quirks—like checking the sharpness by slicing through a piece of paper—helps instantly gauge if the effort was worthwhile. But there's a fine line to maintain here; overzealous testing might wear down a freshly sharpened edge.
Cleaning and Care
Maintaining cleanliness is vital for hand planes, as it significantly influences their performance and resilience against wear. Dust, residue, and moisture can wreak havoc on both the metal and wooden parts of these tools, leading to corrosion and loss of functionality.
Materials for Care
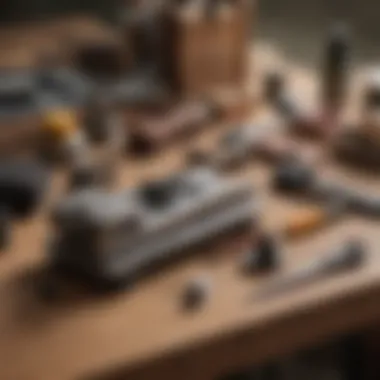
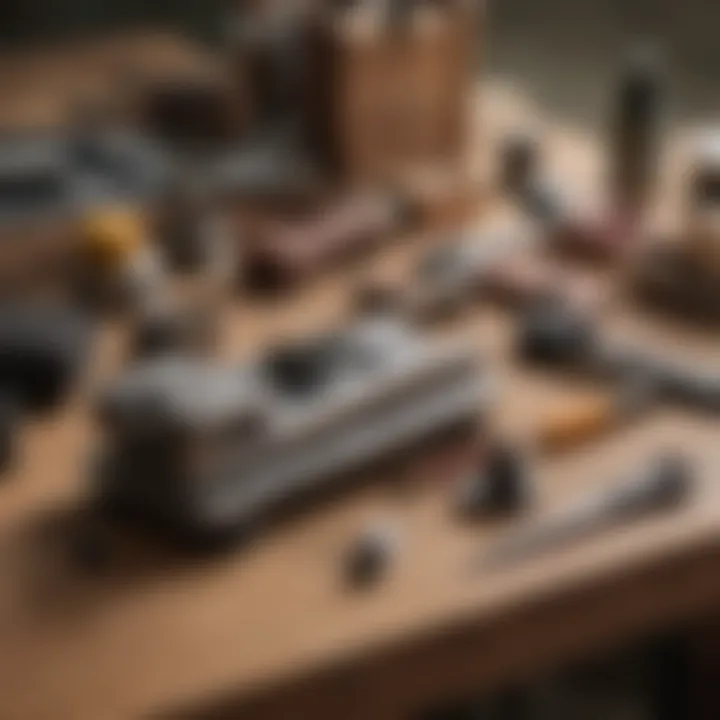
Effective cleaning materials include:
- Steel Wool: For removing rust and surface debris without damaging the metal.
- Non-Abrasive Cloths: Ideal for polishing wood and metal surfaces without scratching.
- Lubricants: Oils such as mineral oil or specialized tool oil can protect against moisture and rust.
- Acid-Free Cleaners: These can remove sticky residues and finish remnants without harsh reactions.
Woodworkers often swear by steel wool for quick touch-ups, as it's gentle yet effective. On the other hand, be cautious—a too-thorough application can dull the surface over time.
Storage Solutions
How you store your hand planes directly impacts their durability and performance. Here are some storage solutions that ensure the tools remain in prime condition:
- Toolboxes with Compartments: Keeps planes organized and separated to prevent nicks.
- Magnetic Holders: For easy access and to avoid clutter, these can securely hold planes while allowing visibility.
- Humidity-Controlled Cabinets: Effective for preventing moisture buildup, which can lead to rust and deterioration.
An organized approach—like investing in a dedicated rack for hand planes—can streamline any workshop. However, the drawback of specialized storage is initial cost and setup time, which may not appeal to all.
"A well-maintained hand plane is like a trusted companion, always ready to deliver on the promise of precision."
Hand Planes in Surfboard Shaping
In the intricate art of surfboard shaping, hand planes take center stage. Their significance lies not just in functional attributes but also in their ability to craft shapes that can make a surfer's ride smoother and more exhilarating. When it comes to carving out contours and profiles, hand planes become indispensable tools for both precision and creative expression. Their unique design and handling capabilities allow shapers to manipulate materials effectively, carving nuanced shapes that serve both aerodynamics and aesthetic purposes.
The Role of Hand Planes
Creating Contours
Creating contours is paramount in surfboard shaping, as it directly influences how a board performs on water. With hand planes, shapers can achieve subtle curves and nuanced shapes that machine tools often fail to capture. The precise control offered by a hand plane allows for adjustments that cater to an individual surfer’s needs. This results in boards that perform uniquely in various surf conditions. A notable characteristic of contouring with hand planes is the tactile feedback it provides; shapers feel the material and can intuitively shape the surfboard for optimal performance.
A beneficial choice, using hand planes for contours can lead to finely tuned edges and surfaces that are superior to factory-made shapes. However, it does come with a learning curve and requires practice to master the necessary techniques.
Achieving Desired Profiles
Achieving desired profiles involves determining how a surfboard will interact with the surf. Hand planes excel in this area by offering precision crafting capabilities, allowing shapers to sculpt outlines that can rage from narrow and pointy to wide and stable. One key aspect of this practice is the customization potential; each board can be tailored not just to type of waves but also to a specific surfer's style.
The unique feature of hand planes in this regard is their flexibility. Unlike factory molds, which are often standardized, hand planes allow for adjustments and iterations until the shaper and surfer both agree on the shape. While gaining proficiency with these tools can be challenging, the personal satisfaction from shaping a board can’t be replicated by other means.
Choosing Planes for Surfboard Shaping
When it comes to selecting the right hand planes for surfboard shaping, understanding specific characteristics is essential.
Specific Characteristics
The specific characteristics of hand planes include blade width, angle, and the type of body construction. Wider blades can manage thicker materials, while narrower blades can offer precision for detailed shaping. A common choice among shapers is the low-angle block plane, which provides versatility and control.
Why is this important? These characteristics directly affect how shapers can manipulate the wooden blanks. The right plane enhances a shaper’s capability to uphold the integrity of their designs, making it easier to carve cleaner contours and achieve smoother finishes. However, shapers must balance these elements with their personal styles and preferences, which can sometimes complicate their choices.
Best Practices for Shapers
Best practices for shapers involve a mix of technique, tool care, and ongoing education. It’s vital for shapers to maintain their tools regularly, ensuring blades are always sharpened and in prime condition. Additionally, attending workshops or joining local shaping communities can foster growth and offer insights into innovative techniques.
Key practices include keeping the workspace clean to prevent material interference and practicing different shaping techniques regularly.
The advantage of adhering to these best practices is clear: they not only enhance the shapers’ skills but also improve the overall quality of the surfboards produced. With better techniques and well-maintained tools, shapers produce boards that perform better and last longer.
"A well-crafted surfboard is not just about looks; it’s a blend of artistry and engineering, and hand planes are the key to achieving that delicate balance."
Hand planes are essential in surfboard shaping, providing a level of personalization and intricacy that mechanical tools simply can’t match. As surfboard shapers continue to revolutionize their craft, hand planes remain a timeless choice, melding tradition with innovation.
Epilogue
As we wrap up this exploration of hand planes, it's essential to reflect on the key elements presented throughout the article. Hand planes are not just tools; they are an embodiment of craftsmanship that marries functionality with artistry. Understanding their various types, techniques, and uses leads to better decision-making for both woodworking enthusiasts and surfboard shapers.
Recap of Key Points
To sum up the insights shared:
- Types of Hand Planes: We've dissected bench planes, block planes, and specialty planes, each serving distinct functions that cater to different woodworking needs.
- Selecting the Right Plane: Factors such as material types and ergonomics come into play, helping users choose a tool that feels right in hand and suits their project goals.
- Techniques and Maintenance: Basic and advanced techniques can elevate users' skills, while proper maintenance — encompassing sharpening and care — ensures tools remain effective over time.
- Surfboard Shaping: The specific application of hand planes within surfboard shaping highlights the unique contours that can be achieved, enhancing performance and aesthetics.
It's intriguing to think about how this traditional tool continues to find relevance in modern crafts. Properly utilized, hand planes are capable of bringing ideas into reality with precision.
Future of Hand Planes in Craft
Looking ahead, the future of hand planes seems promising. As technology advances, there's potential for new designs and materials to emerge, promising increased efficiency and even more ergonomic solutions for users. The fusion of classic techniques with modern innovation may lead to tools that honor traditional methods while catering to today's woodworking trends.
Moreover, as more individuals engage in sustainable practices, hand planes offer a refreshing return to manual methods, reducing the reliance on electric tools. This approach not only connects artisans more closely with their work but may also inspire a renaissance in craftsmanship, particularly among younger generations who value heritage along with modern skillsets.
"Craftsmanship is not just about the final product; it's about the joy of creating with your hands, the satisfaction of mastering a skill, and the connection to the materials you work with."